Sludge Dryer
Sludge Dewatering Equipment
The M.W. Watermark™ Continuous Sludge Dryer is designed for volume and weight reduction of metal hydroxide plating waste.
We hold a commitment to providing innovation for the water and wastewater treatment industry which is well renowned. With that in mind, we are constantly working on improving and redesigning machinery to introduce to the world. The M.W. Watermark Continuous Sludge Dryer reduces waste volume and weight significantly, offering an average yearly savings of nearly 60%.
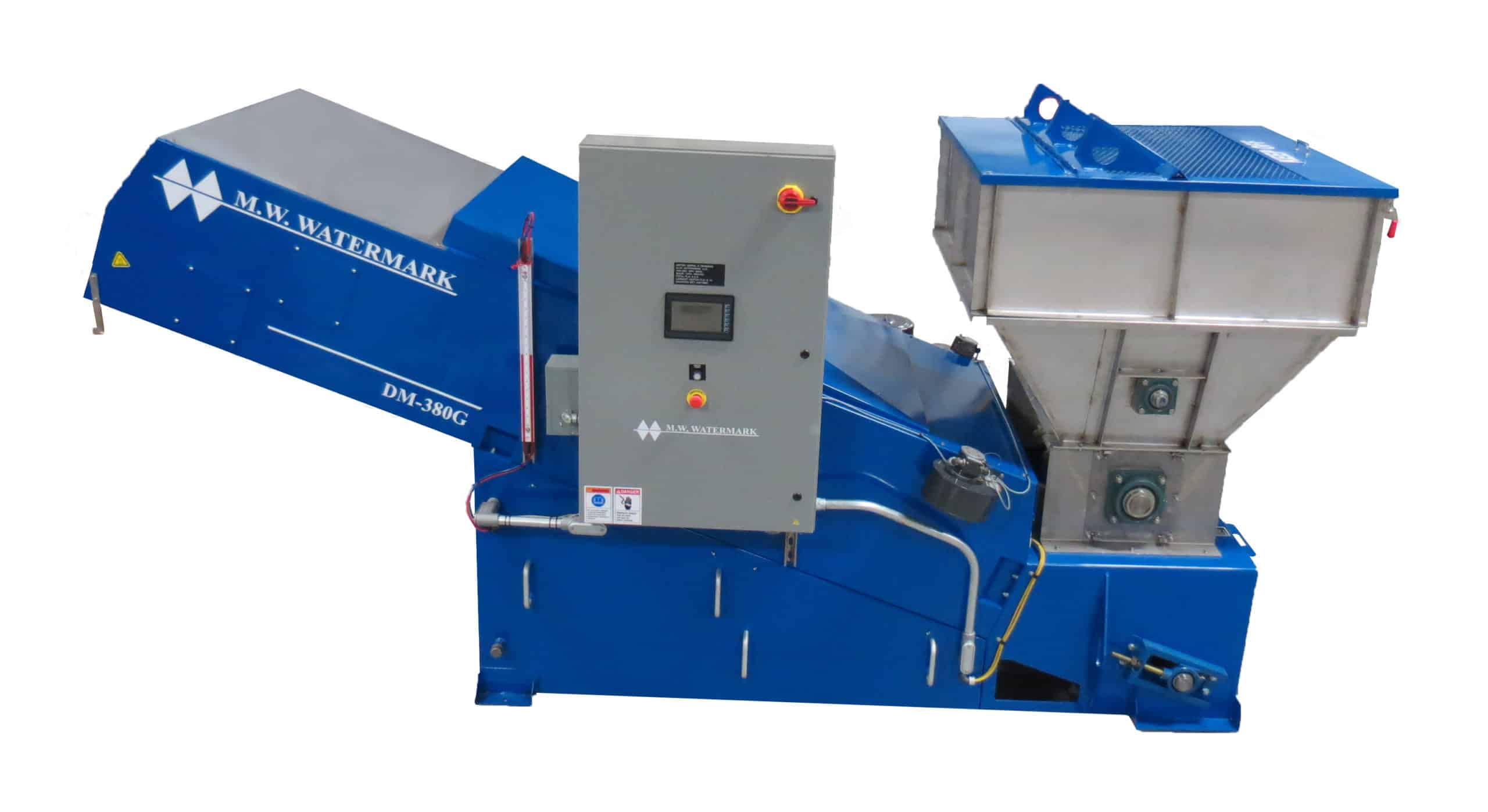
- Description
- FAQ's
- Photos
- Videos
THE M.W. WATERMARK™ CONTINUOUS SLUDGE DRYER
The Continuous Sludge Dryer is designed to process metal hydroxide plating wastes, and when used in conjunction with a filter press, further dries filter cakes and can brings them from approximately 30% solids up to potentially 75% solids.*
*Typical results. Actual results may vary.
Our sludge dryer features several improvements in efficiency and simplicity over other continuous dryers, with a drop-in footprint for compatibility and ease of installation.
These improvements have been designed with our customers’ requirements in mind, and include the following:
- User-friendly PLC with full-color touch screen and fault alarms
- Standard stainless-steel cake hopper
- Easy external service access to high-temperature bearings
- Over-sized extruder gearbox with AC drive and inverter duty motor
- Powder coating of carbon steel components are corrosion resistant
- Durable stainless-steel construction of all wetted components
The Continuous Sludge Dryer is available in two models to best fit your capacity needs: The DM-200G and the DM-380G. Check out the specs in our continuous sludge dryer brochure to determine what model best suits your needs.
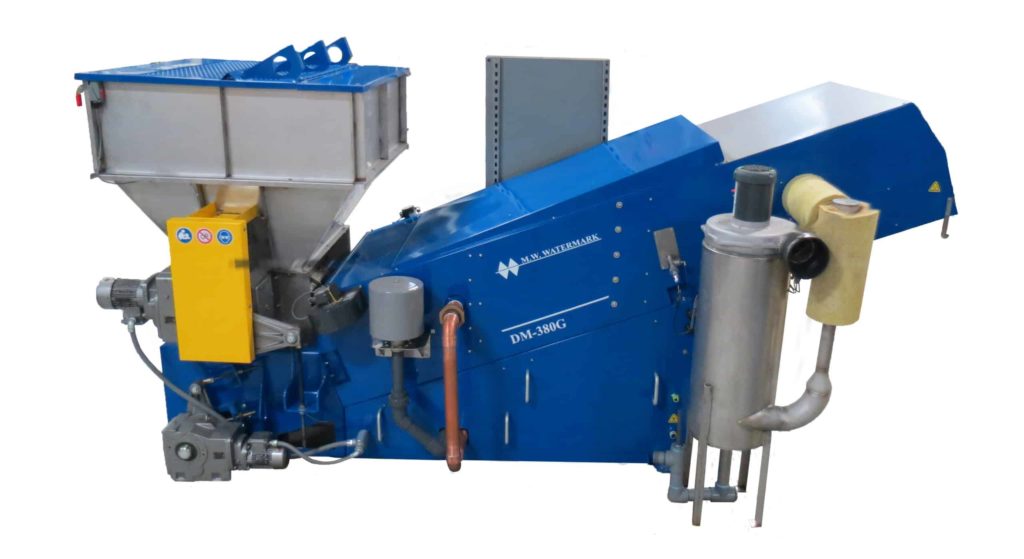
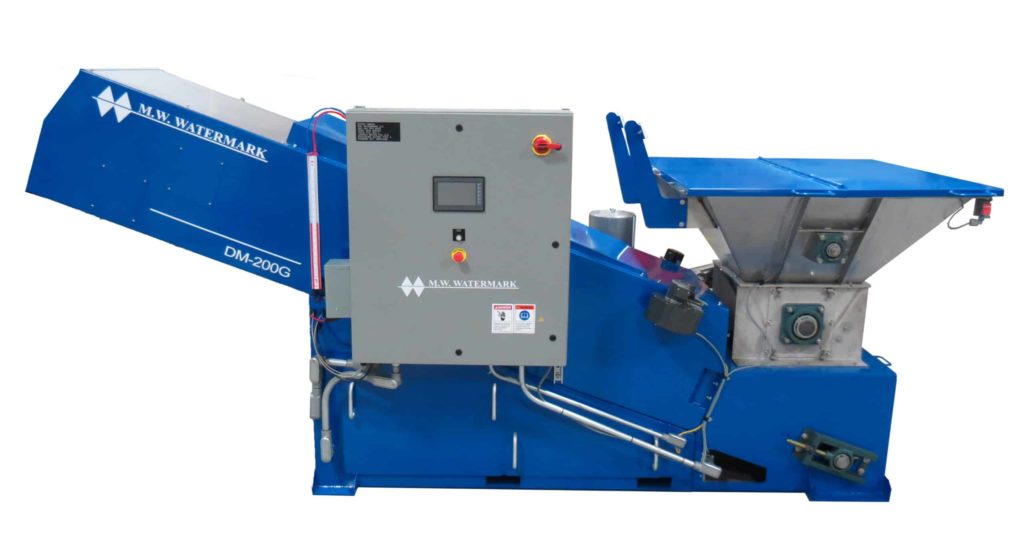
At full capacity, the DM-200G can process up to three cubic feet of material in an hour, while the larger DM-380G can process double that, or up to six cubic feet. These machines are designed to process metal hydroxide plating wastes, and, when used in conjunction with your filter press, are used to dry filter cakes and bring them from 30% solids to up to 75% solids*.
*Typical results. Actual results may vary.
The Continuous Sludge Dryer offers several improvements in efficiency and simplicity over other continuous dryers. These improvements include a drop-in footprint for compatibility and ease of installation, a PLC with full-color touch screen and fault alarms, stainless-steel cake hopper, easy external access to high-temperature bearings, an over-sized extruder gearbox with AC drive and inverter duty motor, and durable stainless-steel construction of all wetted components.
Download our Sludge Dryer Application Data Form to help determine which of our sludge dryers would work best for you. This gives you the option to fill out the form and send it back to us for review.
We also offer maintenance and repair services for our own line of sludge dryers well as models from other suppliers. We continue to offer aftermarket support for other brands of dryers.
Q: How does a sludge dryer work?
Our continuous sludge dryer is designed to be used in conjunction with a filter press, which dewaters metal hydroxide slurries from metal plating operations.
- The filter cake that is produced by the filter press is dumped into the sludge dryer receiving hopper (A).
- Wiper blades push the filter cake through a stainless-steel screen, decreasing the material’s size and shaping it for increased surface-area and efficient drying (B, C).
- Next, the noodle-shaped material falls onto a continuous stainless steel mesh belt, where it passes under a series of infrared heaters for drying (D).
- The heat is produced by natural or LP gas, while ambient air is drawn through the heat chamber by a fan mounted on the inlet of the wet scrubber (E).
- After significant reduction, the dry, granular material exits the dryer into a container for removal.
Q: What parts do you stock for sludge dryers?
M.W. Watermark™ can supply infrared gas burners and other heating system parts including conveyor belts, sprockets, shafts, hoppers & extruders, gas trains, scrubbers, controls, and discharge bags. We stock parts for most brands of continuous dryers!
For more info, check out our Sludge Dryers Parts Brochure.