There are three basic categories of filter press plates: recessed chamber, membrane squeeze (diaphragm squeeze) and plate and frame. Continue reading to learn the differences between each type of design.
Recessed Chamber Filter Press Plates
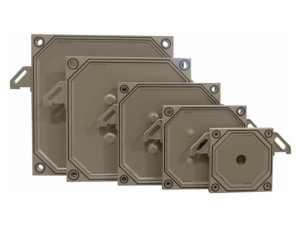
These filter plates are utilized in various brands of recessed chamber filter presses, and represent the most commonly used plate.
- The filter plates are stronger and have a higher fill pressure than plates and frame
- Gasketed, virtually leak free (CGR)
- Allows for mechanical plate shifting
- Non-gasketed available (NG)
CGR vs. NG Filter Plates
“CGR” is an acronym for “Caulked, Gasketed, Recessed chamber.” CGR filter plates should provide a virtually leak-proof filter press. Filter cloths for these plates are octagon shaped, with a caulking rope or cord sewn into the edge of the cloth.
“NG” means “Non-Gasketed.” The NG cloth is faster and simpler to install, though the tradeoff is that occasionally some dripping can happen when using NG cloths.
To learn more about filter cloths, take a look at our filter cloth page.
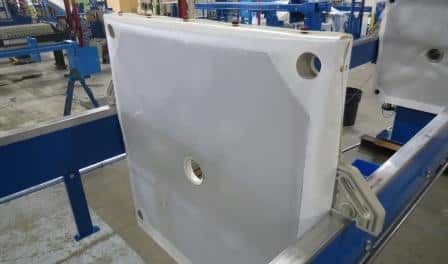
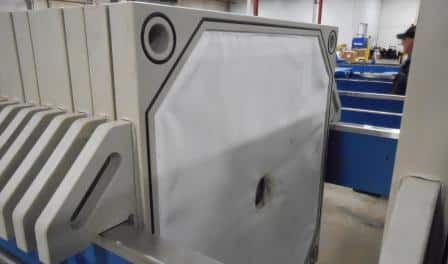
Membrane Squeeze Filter Plates (Diaphgragm Squeeze)

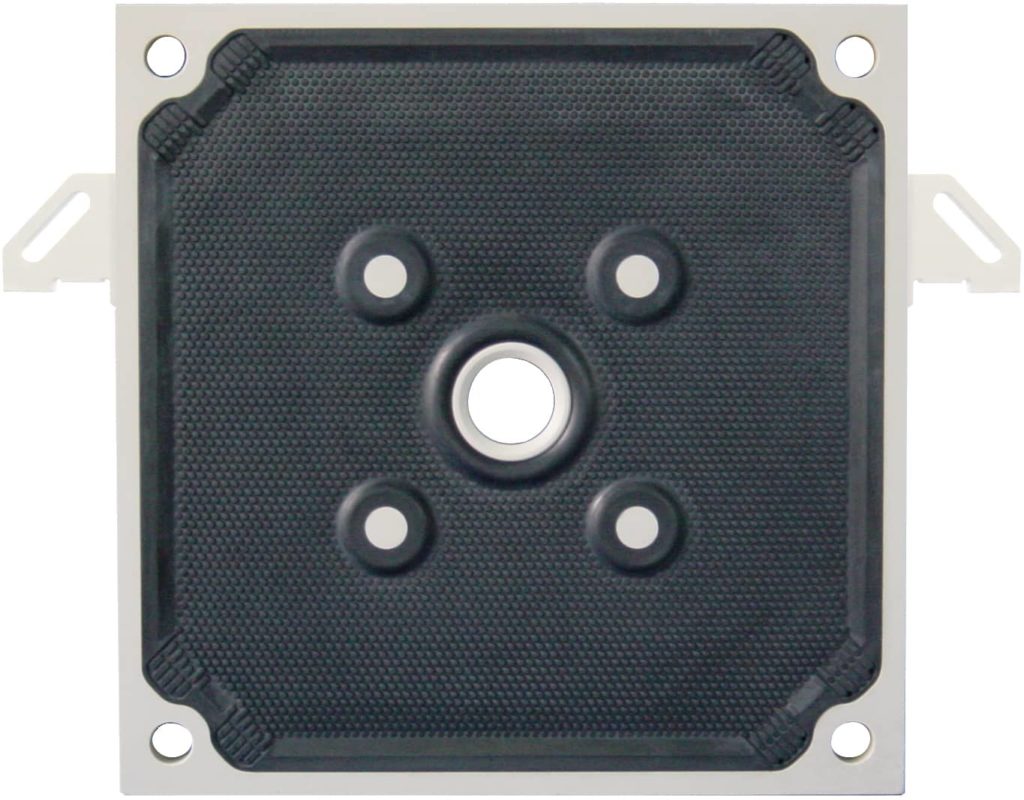
These filter plates are utilized in a membrane squeeze filter press and are designed for unique applications. This type of plate is also more costly than recessed chamber plates. Using diaphragm/membrane squeeze filter press plates may result in significant additional fluid removal and/or cycle time reduction if the filter cake is compressible.
These are considerations that our Sales and Service Team keeps in mind when recommending membrane squeeze plates:
- The filter cake is compressible
- Slurry has higher than average solids
- Time is money – the time saved by the squeeze justifies more expensive equipment
- The slurry has variable volume
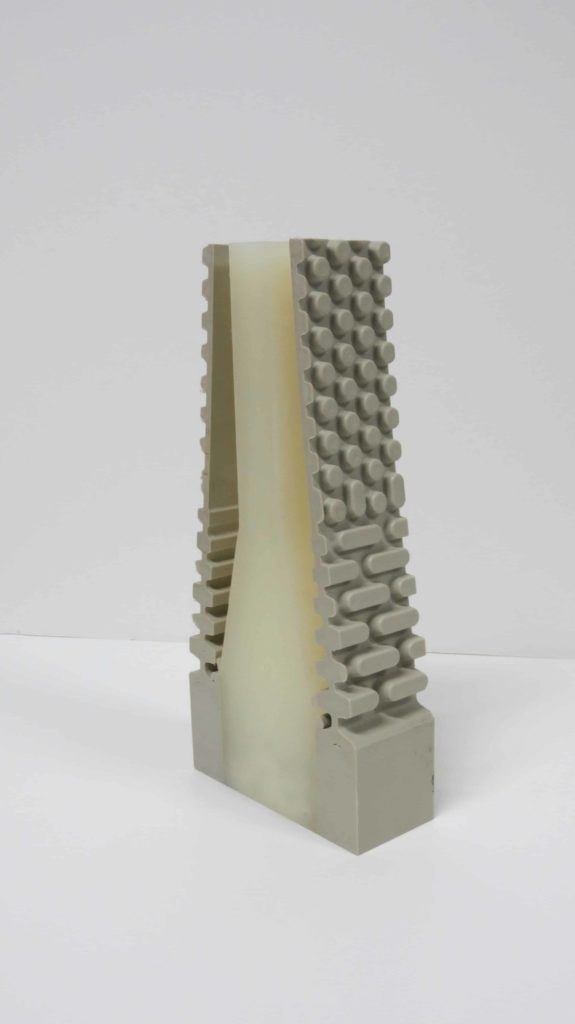
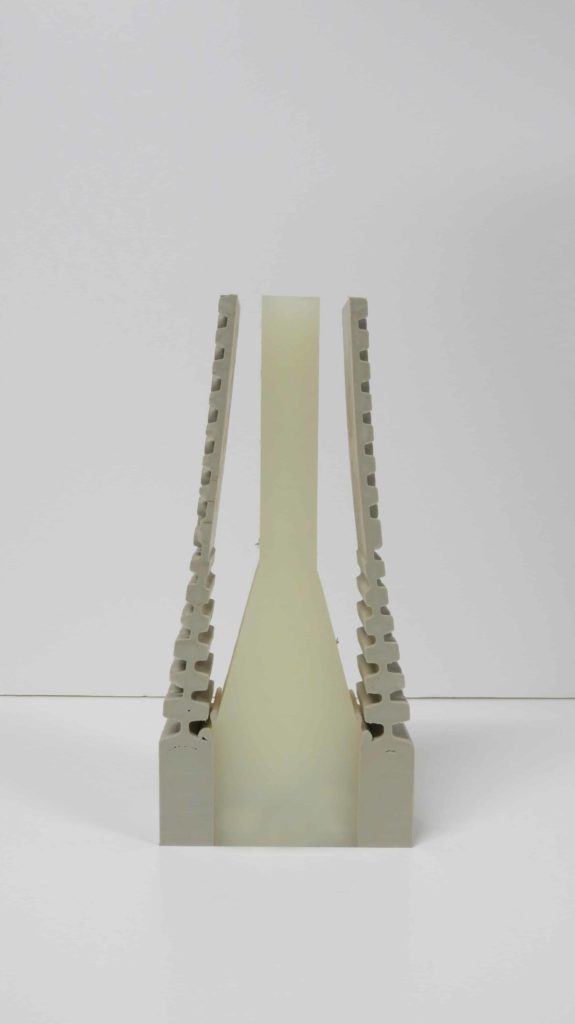
Membrane Squeeze Plate with Welded Diaphragm
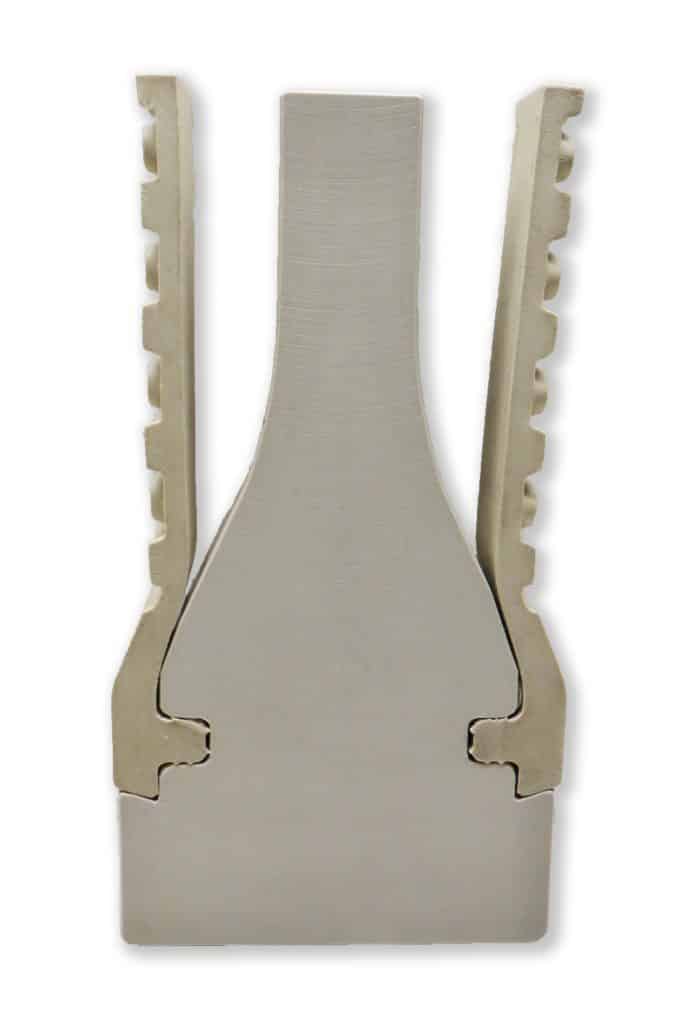
In a typical filter press application, approximately 80% of the solids are pumped into the press in the first half of the cycle, with the remaining half considered the consolidation stage. With membrane squeeze, the cycle is shortened and the cake moisture content is reduced (see chart).
The result is increased throughput and better liquid recovery. Adding membrane squeeze to a filter press requires a specialized plate stack, a squeeze water manifold, and a filter plate pressurization system. Typically, membrane plates are alternated with standard chamber plates in a “mixed pack” as shown in the photo below.
Contact M.W. Watermark to discuss which type of membrane squeeze plate may be best suited for your particular application. If chemical compatibility is a concern, various materials of construction are available for replaceable diaphragms, including EPDM, NBR, Viton, and more.
Plate and Frame Filter Press Plates
Plate and frame is the oldest of the filter plate designs, but is still useful in certain applications.
- Used for fine filtration where filter paper may be required
- Allows for different filter cake thicknesses by adding a thicker or thinner frame
- Filter cloth drapes over plate
- You should expect some leakage
- Operated at lower pressures
- Applications:
- Polishing
- Specialty chemicals
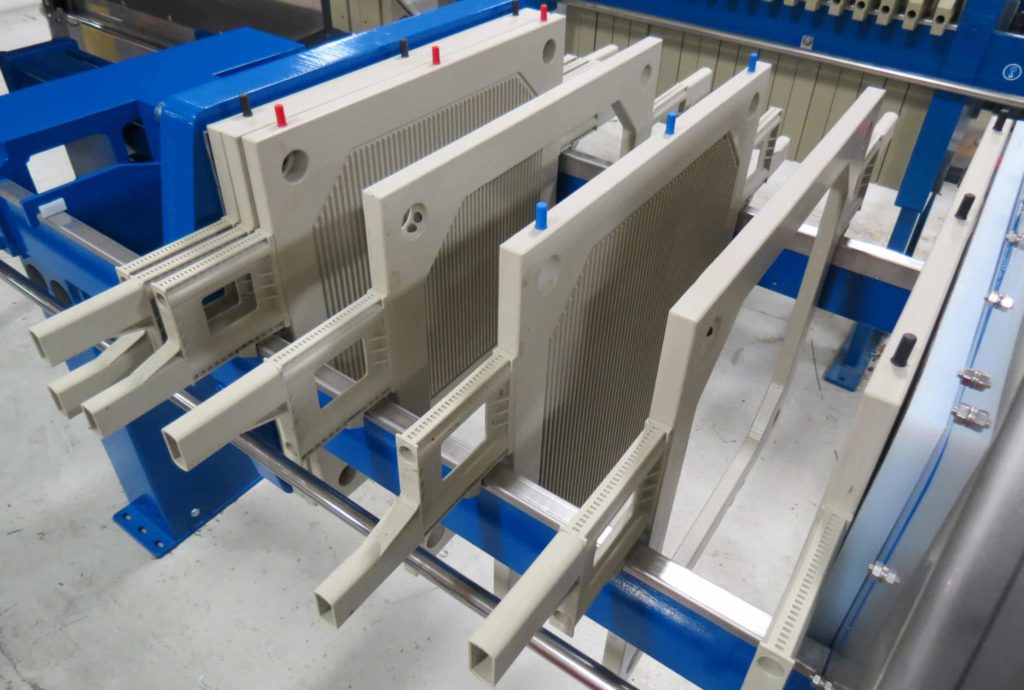
Contact our Sales and Service Team to learn more or request a quote today.
About M.W. Watermark
M.W. WATERMARK wants to make a difference. We are passionate about the world’s water. We are innovative, focused on customer service and always try to exceed expectations. We are an environmentally conscious company with people who are energized, encouraged and inspired to make a difference on our planet by helping to keep our shared, finite water supply clean and usable for generations to come. We build amazing, custom water and wastewater treatment equipment. Together, we can make a difference.